Selective plating process
Selective Plating is almost as old as electroplating itself. Although it has been used for such a long time and quite broadly, it is interesting that many professionals, particularly in mechanical engineering, are unaware of this method. Selective Plating is a cutting-edge mobile method for the electrolytic coating of localized surfaces without the use of electroplating tanks. The same processes take place during selective plating as in traditional electroplating, such as chrome plating in large tanks, but in selective plating, metal is deposited using a cotton brush placed on a graphite anode, which resembles the anode used in traditional electroplating. The cathode, similarly to traditional electroplating, is the item to be coated. The selective plating process applies a metal coating to precisely specified locations and with a precisely specified thickness. The metal coating process is much faster than in traditional electroplating (galvanic deposition), and therefore enables an absolutely precise thickness of the metal coating.
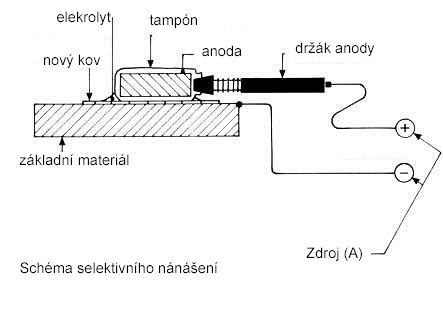
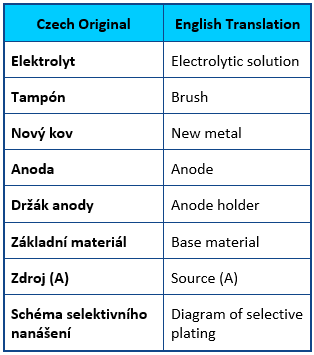
Selective Plating is used for repairs, as well as for the electroplating of new parts. It is used for repairs where the parts are mechanically damaged – scratches, dents, holes or damage due to corrosion or wear and tear. The scope of use of such repairs is very broad. These repairs can save parts that would otherwise have to be manufactured anew at great cost and with a certain period of time required for their production. If, for instance, scratches appear on a piston rod with a depth of 2 mm, it is not possible to repair it conventionally, because it would be extremely expensive and technically infeasible. Imagine that it would have to be ground by 2 mm in radius, and then it is basically impossible to achieve the original size using traditional electroplating. In such case, either a combination of micro welding and brush electroplating is used, or only brush electroplating – both approaches are possible. In the former case, the defect would be partially built-up by micro welding and the hole would be filled, and then the rest of the metal coating would be performed using the selective plating process, or the hole would first be filled with one material, and the rest would then be filled up to the original size using the same selective plating method. The selective plating equipment is mobile, which makes it possible to carry out repairs on site, as well as in parts built into various machines and equipment.
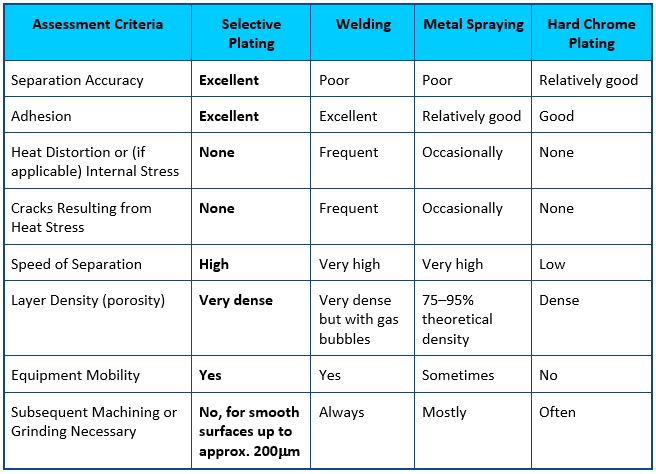
Areas of Application
Selective Plating is used in various industries, just like chrome plating is used for manufacturing in various mechanical engineering sectors. Selective Plating is used exclusively, for example, for the maintenance of certain parts of all aircraft throughout the world. All aircraft repair shops in the world exclusively use selective plating for the maintenance of landing gear, as well as of other parts; the same applies to the production of these parts in the aviation industry.
Selective Plating is commonly used for on-site repairs in the cellulose and paper industry. Typical applications include the diameters of bearings of suction rolls, diameters of bearings of the drier heads, repairs of surface defects caused by maintenance, bearing bushes in pumps, openings of impellers, shaft bearing journals and sealing surfaces, bearing bushes in electric motors, rotor journals, collectors and bus bars. In power generation plants, this method can be used for repairs of steam turbine bearing journals, flange joints, cylinder liners of diesel engines, connecting rod openings and crankshaft journals.
Selective Plating is almost exclusively used for repairs of rolls in printing and paper machines, where the repairs are carried out without disassembly directly on the rolls of these machines.
Selective Plating is also used in the chemical and petrochemical industries, where it enables quick and cost-effective maintenance cycles. Thanks to the use of this process, maintenance technicians can repair pumps, engines, flanges, valves and other parts on site by applying the metal to the components without the heating or deformations caused by welding or thermal metal spraying. This type of plating is 60 times faster than dip coating, and is real electroplating, so the metallic bond is basically atomic, which results in excellent adhesion in comparison to other processes.
Selective Plating is also used in the energy sector. Typical applications include silver-plating of the sets of palm buttons, reactance winding, copper wedges and strips and the coating of shafts and motor parts. It is mainly used for achieving a reduction in transfer resistance and for better resistance to wear and tear.
Selective Plating is also used in the railway industry, particularly for the modification of the sizes of worn journals of axle rolling-contact bearings, and for the restoration of the sealing surfaces of friction rings, for the restoration of excessive bearing cones, repairs of cavities, dents and defects of hydraulic and sealing surfaces, and the restoration of worn bearing seals, bearing saddles and caps. These are just a few examples of possible application. The use of this technology is very universal and broad.
Examples of damage
Repair process
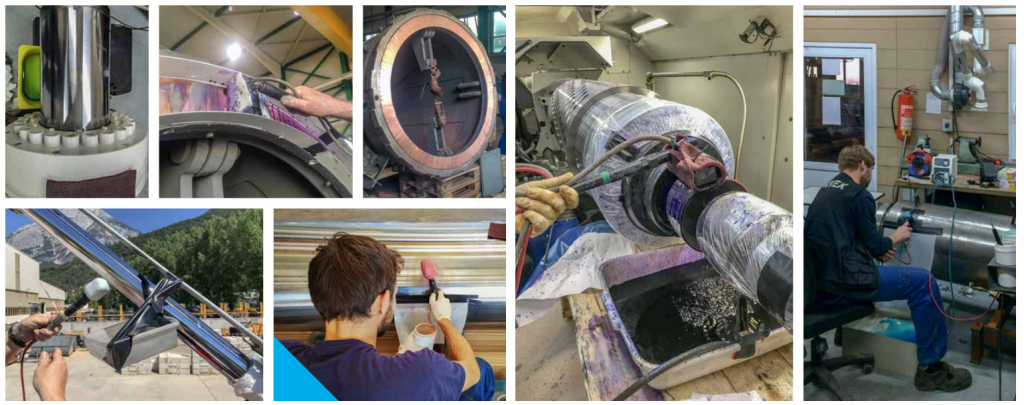
From damaged to repaired state
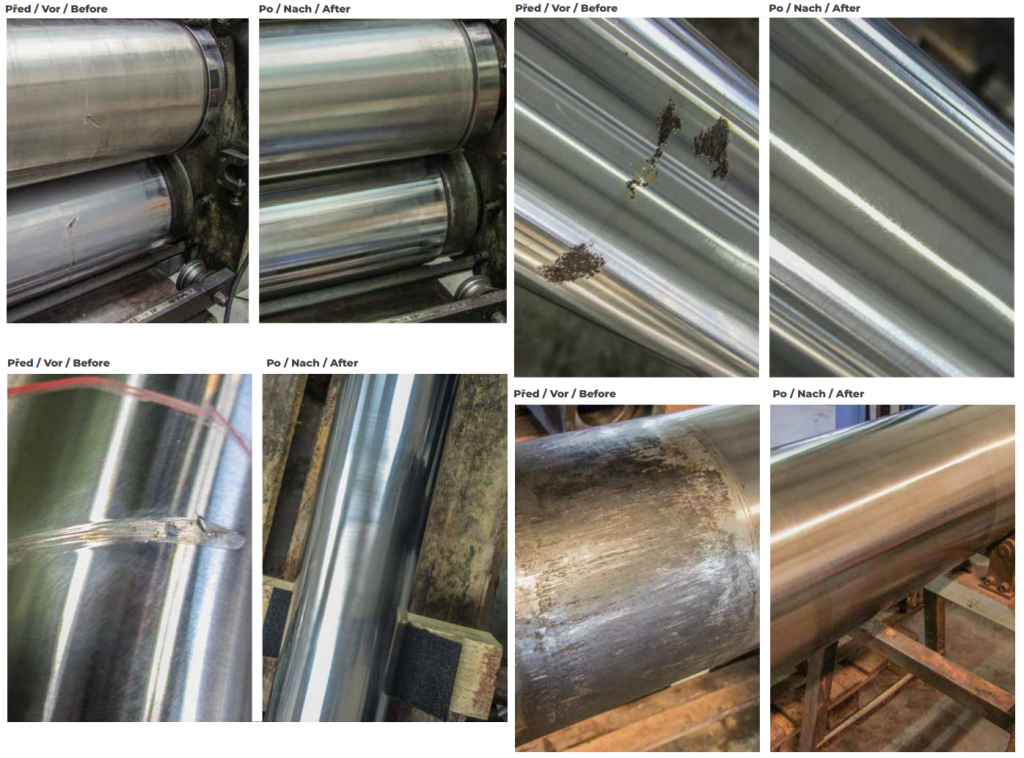
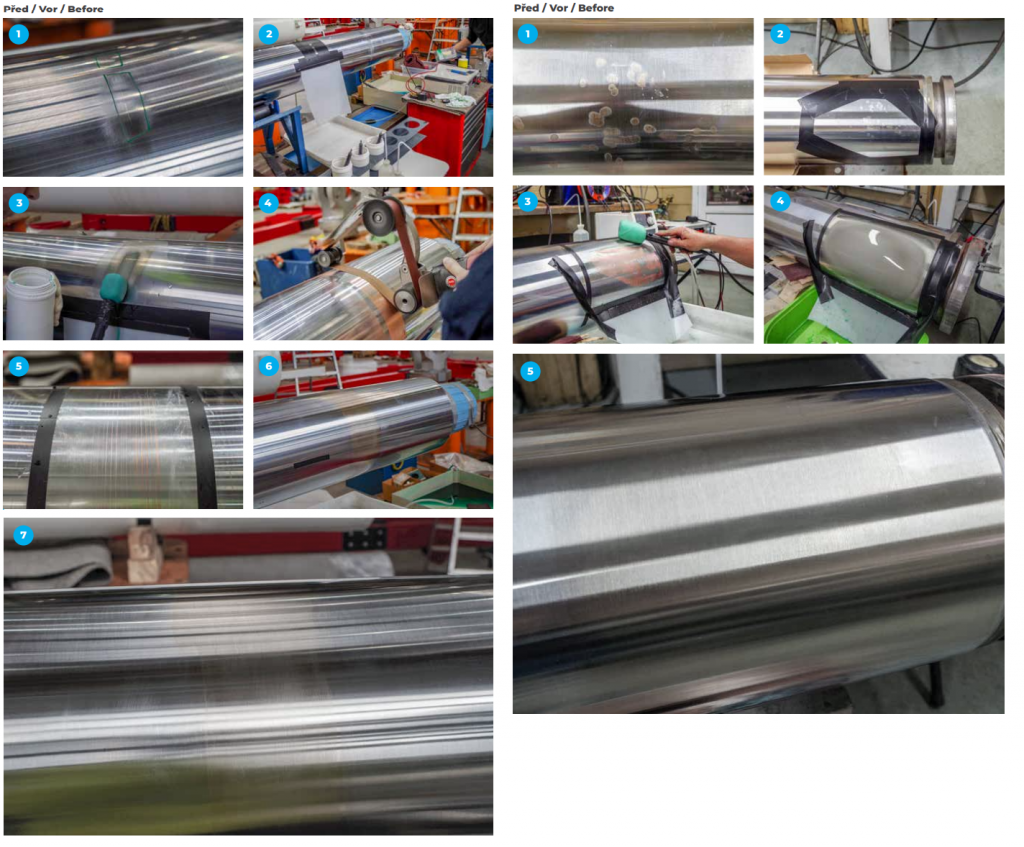